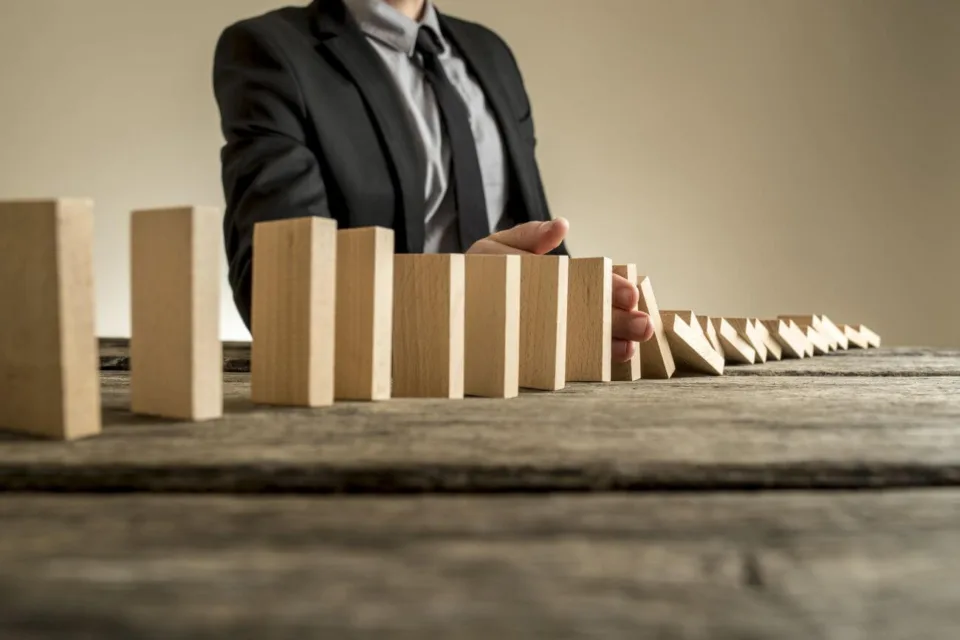
Chcesz udoskonalić wykorzystywany proces, a może planujesz wdrożenie nowego? Metoda FMEA zapewnia wsparcie w każdej fazie procesu. Wskazuje na potencjalne wady i związane z nimi skutki. Sprawdź, dlaczego warto korzystać z analizy FMEA.
FMEA to analiza związków przyczynowo-skutkowych między rodzajami a konsekwencjami potencjalnych wad. Kompleksowość metody umożliwia zdefiniowanie ryzyka, a tym samym określenie odporności procesu bądź produktu na usterki. Systematyczność i interdyscyplinarność sprawiają, że koncepcja FMEA zapewnia zrównoważony proces produkcyjny. Wpływa na jego efektywność wbudowując środki kontroli jakości na wszystkich etapach.
Analiza FMEA, czyli jak zapobiegać powstawaniu potencjalnych wad produktu
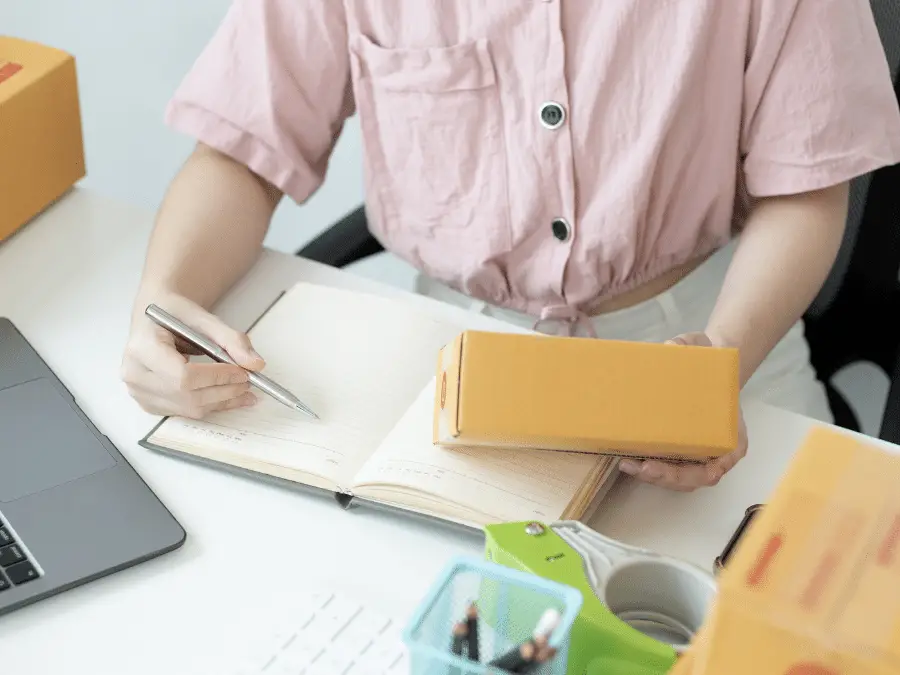
FMEA to pojęcie, które w biznesie zostało zaadaptowane się w latach 60. ubiegłego wieku. Jednak ta metoda swoje korzenie miała już w latach 40. czerpiąc z zarządzania dla systemów wojskowych. Początkowo stosowana w USA metoda kontrolowania jakości służyła do weryfikowania projektów elementów statków kosmicznych (NASA). Przeprowadzenie FMEA miało zwiększyć bezpieczeństwo uczestników wyprawy. Następnie analiza znalazła zastosowanie także w przemyśle jądrowym i lotniczym.
Na przełomie lat 70. i 80. analiza przyczyn możliwych błędów rozprzestrzeniła się również w Europie. Korzystał z niej między innymi:
- przemysł chemiczny;
- przemysł elektroniczny;
- przemysł samochodowy.
Lata 90. przyniosły zaadaptowanie FMEA w ramach normy ISO: ISO 9000 i QS-9000. Ze względu na najwyższy poziom niezawodności stała się nieodłącznym elementem prowadzenia działalności w największych sektorach biznesu.
FMEA – definicja
Analiza FMEA (z ang. Failure Mode and Effect Analysis) określana jest także jako FMECA (ang. Failure Mode and Criticality Analysis) czy AMDEC (fr. Analyse des Modes de Défaillance et Leurs Effets).
Polskie znaczenie tej metody przybiera różne rodzaje. Może to być analiza:
- rodzajów i skutków wad;
- możliwości powstawania i efektów wad;
- możliwych przyczyn i skutków wad.
Analiza rodzajów i skutków potencjalnych błędów ma zapobiegać skutkom wad procesów i produktów. Mogą one występować na etapie projektowania lub produkcji. Jakościowa analiza niezawodności umożliwia przewidzenie ryzyka wystąpienia wad, ocenę ich konsekwencji oraz identyfikację i eliminację przyczyn. Zapobieganie potencjalnym wadom możliwe jest dzięki dostarczaniu ro całego procesu produkcji masowej.
FMEA – podstawowe założenia:
- ok. 75% błędów jest skutkiem nieprawidłowości na etapie przygotowania produkcji;
- ok. 80% błędów zostaje wykryte na etapie produkcji, kontroli produkcji i w okresie eksploatacji.
Metoda FMEA – zakres zastosowań
Zastosowanie FMEA to:
- optymalizacja produktu;
- optymalizacja procesu;
- zarządzanie ryzykiem.
Metoda analizy jakościowej określa możliwe rodzaje i skutki błędów pozwalające zoptymalizować produkt:
- na etapie projektowania;
- przed wdrożeniem do produkcji;
- na późniejszych etapach.
Najlepsze wyniki FMEA przynosi w trakcie projektowania produktu, kiedy wprowadzanie niezbędnych zmian korygujących jest najłatwiejsze. Przed wdrożeniem do produkcji efekty są bardziej ograniczone. Wynika to z gotowego projektu, który utrudnia dokonywanie zmian. Kiedy parametry produktu zostały już ustalone, analiza daje bardzo ograniczone rezultaty. W takich przypadkach, metoda FMEA powinna zostać wykorzystana przed następną aktualizacją.
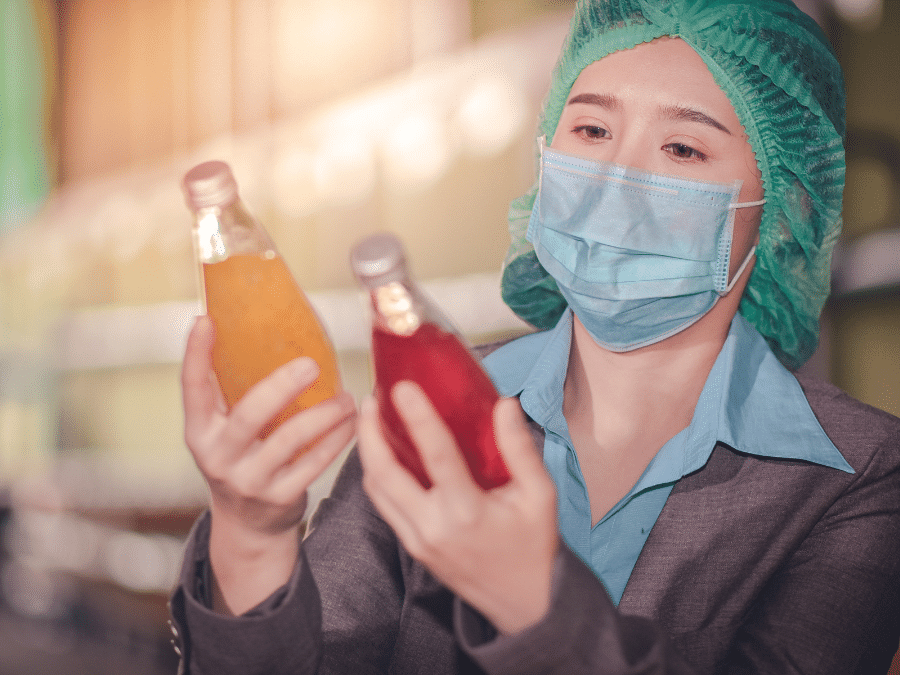
Optymalizacja procesu za pomocą analizy FMECA jest możliwa, gdy firma planuje:
- wdrożenie nowego procesu;
- doskonalenie procesu już istniejącego.
Modelowa sytuacja dla zarządzania jakością to nowe procesy, które można przygotować od podstaw. Niestety zdarza się to dość rzadko. Inną opcją jest analiza istniejących procesów, które dzięki temu zyskają na efektywności.
Analiza FMEA wspiera również zarządzanie ryzykiem. To prosty sposób na rozpoznawanie ryzyka i sposobów postępowania w jego obliczu. Jest wystarczająca zarówno dla małych, jak i średnich przedsiębiorstw.
Nowe zastosowania FMEA
Dzięki metodzie FMEA przedsiębiorstwa mogą udoskonalać wytwarzane produkty i przeprowadzane procesy. Uniwersalność analizy sprawia, że wciąż znajduje ona nowe zastosowania. Wpływają na to także nowo powstałe koncepcje zarządzania produkcją takie jak lean manufacturing.
Współcześnie FMECA wykorzystywana jest w trakcie powstawania koncepcji produktów. Pozwala to na ustalenie, czy plany uwzględniają oczekiwania klientów. Na etapie wytwarzania sprawdza się przy kontrolowaniu realizacji przygotowanych przez technologów specyfikacji. W fazie montażu umożliwia nadzorowanie zgodności procesu montażu ze specyfikacjami. Z kolei podczas organizowania serwisu stosuje się ją, aby sprawdzić zbieżność produktu z oczekiwaniami klientów.
Szerokie zastosowanie powoduje, że FMEA wykorzystywana jest dla takich produktów i procesów jak:
- nowe wyroby;
- nowe procesy;
- punkty bezpieczeństwa i punkty strategiczne produktu;
- poważne inwestycje;
- zmiany technologiczne;
- organizacja serwisu.
Etapy wdrażania FMEA
Przeprowadzenie analizy rodzajów i skutków wad wymaga zebrania odpowiedniego zespołu specjalistów. Trzeba określić zakres FMEA i oszacować ryzyko wystąpienia awarii. Wskazując punkty, które wymagają działania można zaplanować poprawki i wprowadzić je w życie. Ponowna ocena sytuacji pozwoli określić, jak aktualnie przebiegają procedury i jakie jest ich ryzyko.
Wdrażanie FMEA odbywa się w kilku etapach:
- identyfikacja elementów produktu/procesu;
- wykaz możliwych wad lub błędów w produkcie/procesie;
- wykaz możliwych skutków wad lub błędów;
- wykaz możliwych przyczyn wad lub błędów;
- analiza możliwych wad lub błędów;
- ocena ryzyka popełnienia wskazanych wad lub błędów;
- plan działań zapobiegawczych;
- wdrożenie działań zapobiegawczych oraz zbadanie ich skuteczności.
Rodzaje FMEA – FMEA procesu a FMEA produktu
FMEA to analiza pozwalająca na ocenę jednego z trzech obszarów. Są nimi:
- system;
- projekt;
- proces.
FMEA systemu dotyczy awarii, które mają wpływ na system operacji przedsiębiorstwa. Takie badanie obejmuje relacje zachodzące pomiędzy podsystemami oraz integrację tych podsystemów z systemami zewnętrznymi.
FMEA projektu obraca się wokół ewentualnych wad produktów. Mogą one wynikać z wielu czynników, na przykład z charakteru projektu, defektu części składowych czy integracji z pozostałymi produktami.
FMEA procesu skupia się na wadach wpływających na jakość w fazie wytwarzania produktów. Takie niedociągnięcia obniżają niezawodność procesu i mogą powodować niezadowolenie klienta. Ich powodem są zmienne czynniki ludzkie, niemiarodajne wskaźniki procesu czy niestandaryzowane praktyki produkcyjne.
Czy warto wdrożyć metodę FMEA?
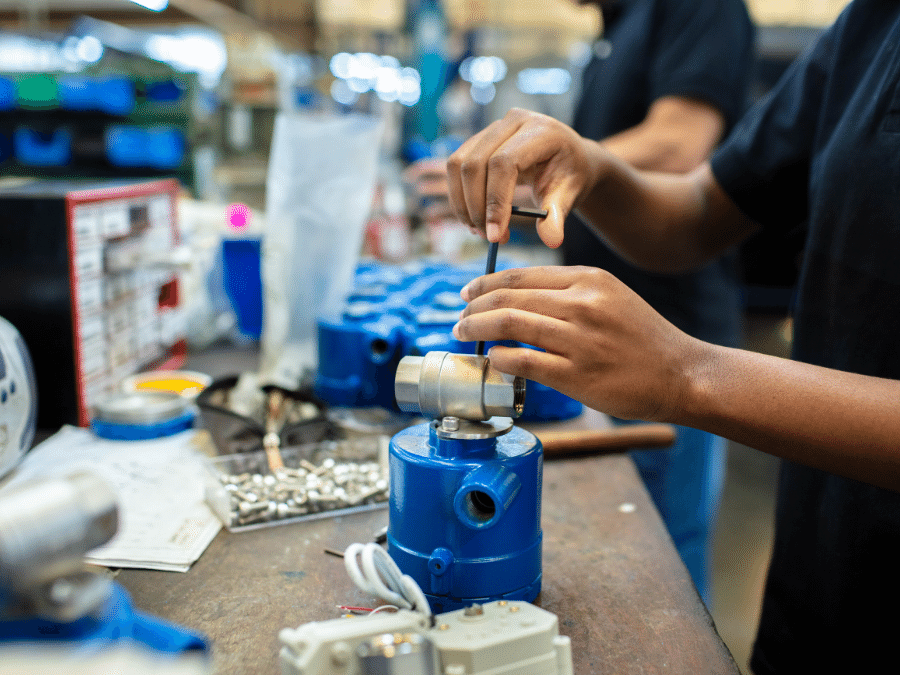
Metod FMEA to optymalne rozwiązanie, dla firm, które chcą zadbać o właściwe zarządzanie jakością. Proces analityczny to nie tylko zapobieganie i usuwanie skutków wad. Ułatwia systematyczną kontrolę jakości usprawniając wdrażanie nowych rozwiązań. Pozwala to zwiększyć wydajność procesu jednocześnie obniżając koszty. Wpływa na łatwość zarządzania procesami i ich niezawodność. Ostatecznie poprawne oszacowanie wielu zmiennych niweluje skutki ewentualnych błędów, które mogłyby powodować na przykład niezadowolenie klienta.
Niestety, pomimo popularności, FMEA ma także wady. Jest to przede wszystkim konieczność przeszkolenia pracowników oraz zaangażowanie kierownictwa. Trzeba też pamiętać, że jest to pracochłonna procedura mająca swoje ograniczenia czasowe.
Powszechne zastosowanie FMEA jasno wskazuje, że wdrożenie procesów analitycznych przynosi pozytywne rezultaty. Metoda ta pozwala uzyskać takie informacje jak:
- prawdopodobieństwo pojawienia się wad;
- prawdopodobieństwo niewykrycia wad przed dostawą produktu;
- znaczenie skutków możliwych błędów z punktu widzenia klientów.
FMEA i FMECA jako metoda zarządzania jakością
FMEA to jakościowa metoda zarządzania produkcją odnosząca się do nowych produktów i procesów oraz do tych już istniejących. Wskazaniem do wykonania analizy jest chęć doskonalenia wszystkich składowych wchodzących w skład działalności firmy. Ustalenie potencjalnych błędów, ich skutków oraz związanego z nimi ryzyka możliwe jest zarówno w produkcji, jak i w fazie projektowania.
Korzyści wynikające ze stosowania analizy możliwych błędów i ich ciągu przyczynowo-skutkowego znacząco wpływają na funkcjonowanie przedsiębiorstwa. Ujednolicony proces kontroli jakości zapewnia wzrost wydajności przy jednoczesnym obniżeniu kosztów. Atmosfera wykreowana w firmie, fachowa wiedza stworzenie banku danych i przewidywanie ryzyka zwiększają funkcjonalność procesów.
FMEA należy do tych koncepcji, które wymagają zaangażowania całej organizacji. Niezbędne jest poparcie kierownictwa i szkolenia pracownicze. Definiowanie ryzyka możliwe jest dzięki pracy grupowej oraz kompleksowości stosowania metody. Wzrost zaangażowania pracowników w sam proces optymalizacji dodatkowo ułatwia doskonalenie istniejącego procesu. Jest to możliwe między innymi dzięki koncepcji KAIZEN. Zakłada ona włączenie w doskonalenie obszarów organizacji wszystkich jej pracowników.
Najczęściej zadawane pytania
Co to jest FMEA?
FMEA to skrót od „failure mode and effects analysis”, co oznacza „tryb awaryjny i analiza efektów”.
- Cykl życia produktu – czym jest i jakie fazy się na niego składają?
- Czym jest benchmarking?
- Zarządzanie projektem i zadaniami członków zespołu – praktyczny poradnik
- Koncepcja lean management jako sposób na optymalizację działań w przedsiębiorstwie
- BPMN, czyli Business Process Modeling Notation – czym jest proces biznesowy?